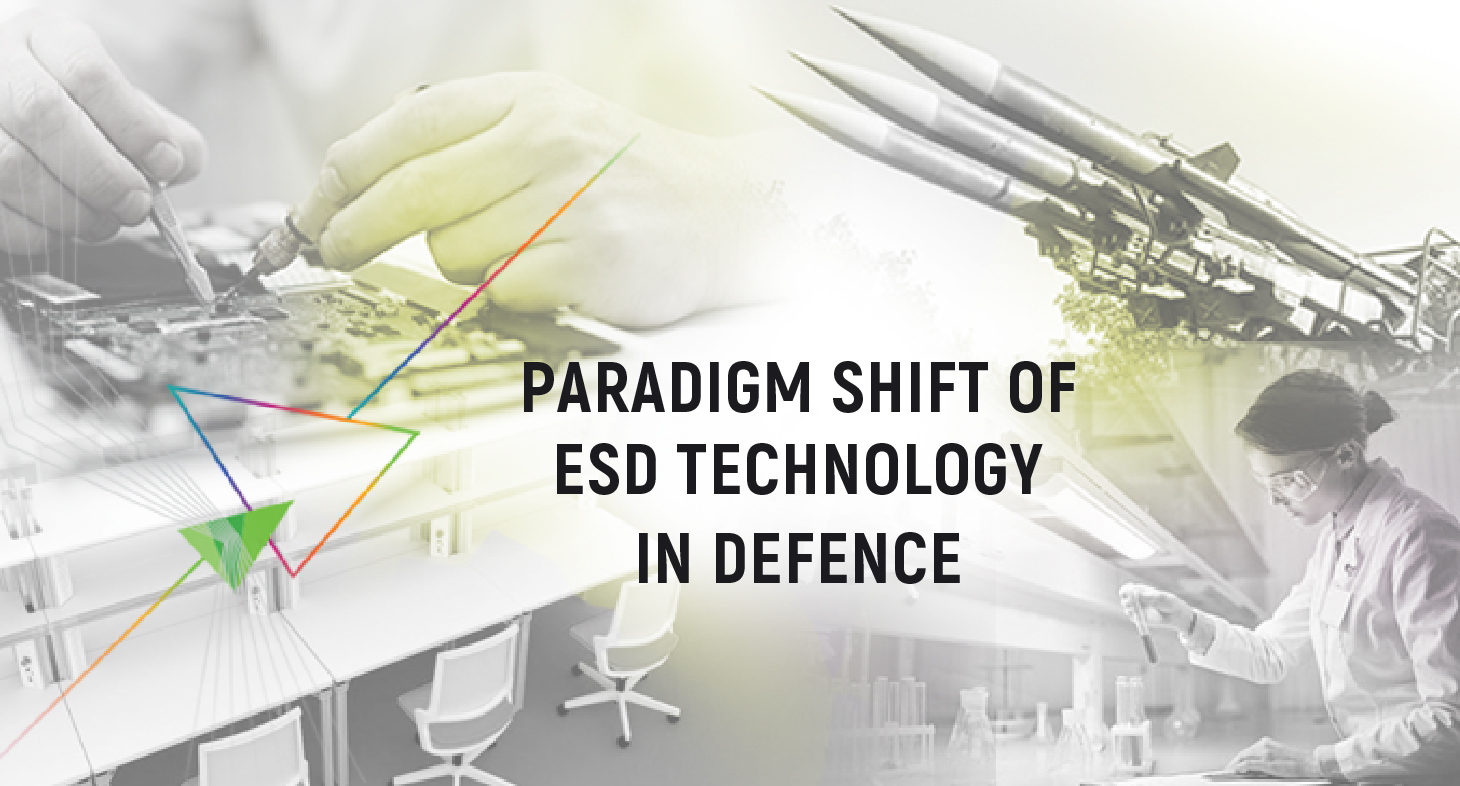
Paradigm Shift of ESD Technology in Defence
Electro-static charge is an invisible menace that lurks inside your electronics production areas, including zones dedicated to Research and Development, Manufacturing, Testing and Storage.
Very simply, Electro-static charge accumulated on the work surface area damages electronic PCB assemblies and microprocessors, memory chips and other high impedance components which come in contact with it.
We need highly efficient Electro-static dissipative surfaces and work areas where these sophisticated electronic components are used.
Defence microelectronics is very demanding in terms of the complexity and density of the microprocessors and high impedance circuitry in the PCG hardware. The constant evolution of warfare tactics has led to massive restructuring of radar, telematics, propulsion and many other systems used in varied military and space applications. If compared to their earlier versions, these systems are now more refined, compact and include highly sophisticated electronics. This intricacy and miniaturization of electronic components has made them more susceptible to ESD damage during any phase of manufacturing or testing.
Electro-static accumulated charge, can damage and destroy intricate construction of today’s miniature electronic components and render them useless. Apart from causing varying degrees of inconveniences to the customer, failure of an electronic component in critical applications like telematics of a missile or space shuttle, radar system of a tank or submarine in the field might result in loss of lives. Industry estimates mention 8% to 33% losses as a direct result of Electro-static damage. Thus, non dissipated Electro-static charge, imposes an unacceptably high cost to the bottom-line and addressing these issues is imperative for any defence and space related organization.
Electro-static Prevention and ESD Protection are thus vital to improving reliability and reducing defects in today’s defence electronics manufacturing facility. The good news is that Electro-static prevention and control is easy and sustainable with the advent of new technology that is driving managers to use fail-safe ESD products in their assembly, manufacturing and testing tables and stations.
Traditional technology used to enable Electro-static Discharge (ESD)
What is traditional ESD technology?
Products such as ESD matting on workbenches, chairs fabric coated with ESD sprays are presently used in defence areas where semiconductor and PCB assembly and testing is carried out for electronic products to be used in applications related to radar testing, missile manufacturing, missile electronics testing etc.
These traditional ESD measures enable the working area surfaces to be dissipative, but not with the same efficiency and reliability that we will describe in the forthcoming paragraphs – “New ESD technology” .
The traditional methods of ESD mats and ESD sprays were OK till the 90’s, an era where the electronics components were simpler and the PCB assemblies were not so dense and complicated.
Problems of using traditional
technology
While traditional technology was widely used till recent times they definitely had many pain areas, such as –
- Products using traditional technology are susceptible to frequent failures and thus need to be monitored on a regular basis. This requires allocation of resources and thus reduces productive time of employees.
- ESD mats which are placed on top of a regular table often wear out within 6-7 months due to usage and need timely replacement. This increases the cost and also poses a danger of working with non-ESD safe work surfaces when the ESD mat has reached the end of its life cycle.
- ESD or Anti-static sprays, commonly used on chair surfaces to make them ESD safe do not last long as their ESD properties wear out quickly, mostly within a few months and then the customer is exposed to working with ESD unsafe chairs and work surfaces. If there is an accumulation of Static electricity, it can lead to major damages to the electronics being tested or assembled.
- Traditional ESD mats and ESD chair fabrics cannot be cleaned because any cleaning method will partially or completely destroy the ESD properties. The table mats and chairs have to be kept just as they are and the production and testing set-up may not look very tidy and clean.
What is new age ESD technology?
New age ESD technology involves use of Volumetric ESD products for both the table and chairs. This technology is causing a paradigm shift in how managers used to approach ESD safe designs and products. With the use of volume ESD, users are guaranteed ESD-safe properties for a lifetime. Let us understand what exactly Volume ESD is.
Volume ESD as used on table and shelf tops, means embedding carbon polymers along with the base material used to manufacture the ESD product. This essentially means that with volume ESD, the properties for discharging the charge are present throughout the volume of the material as compared to its presence only on the contact surface in traditional technology.
For instance, Volumetric ESD in workbench is when the wooden laminated worktop is integrated with conductive carbon polymers, which makes the entire worktop conductive with dissipative lamination on both the sides of the workstation. This is a technology which ensures lifetime ESD protection of the workbench.
In the above image you can see that the worktable laminate is embedded with conductive carbon polymers with lamination on both sides of the workstation, unlike normal wooden worktop which is medium-density fiberboard.
Similarly, this technology can be used to manufacture Volume ESD Polyurethane chairs where the base material of the seats and backs of the chair; which is Polyurethane, is embedded with ESD particles throughout the volume.
All the products mentioned above are used in making world class ESD work tables and ESD chairs which are tested as per IEC 61340-5-1 safety standards. These standards are mandatory for use in all international quality Electronic laboratories and Electronic manufacturing facilities.
Benefits of using new technology
Volume ESD is beneficial over traditional ESD in many ways such as –
- It guarantees lifetime fail-safe ESD properties of the product which means that the chances of ESD failure is negligible. This saves customers, costs in repairs, warranties and replacements.
- Even after wear and tear, the ESD properties remain homogeneous throughout the material. This essentially means that the product, like workstation or chair, will have the same ESD properties effective throughout. Thus rather than concentrating on whether ESD properties of the work tables and chairs are working fine, the user can now concentrate on his testing and assembly and other matters. This improves efficiency and productivity and provides a big relief to the Production and Testing line managers as now they can rest assured that they will have no problems with Static electricity.
- The use of unreliable ESD mats is avoided by the use of volume ESD technology on the wooden table tops. It saves the customer the hassle and repeated capital costs of replacing the mat every 6-7 months.
- Volume ESD products are resistant to regular cleaning agents like IPA, Ethanol and other chemicals. The products do not lose any ESD properties due to cleaning. Thus the work area can be kept neat and clean, in turn improving employee productivity and motivation.
Case Study
A senior scientist, head of Power Electronics division of a government Laboratory in Cochin talks about shifting from old ESD technology to new technology.
This senior Scientist had issues with Electro-static failures during testing of various electronic hardware and PCB assemblies. He also faced severe productivity issues, as most of the employee time was being utilized in wondering why the electronic components were failing without any reason.
Our customer, the senior Scientist, wanted to make his lab with world-class technology and found that by using these new technology products for his work tables and chairs, the volumetric ESD properties were well worth the investment. This new technology guarantees him lower Electro-static failures and the improved ergonomics of the new ESD chairs improves the productivity of his employees.
Currently, as per the senior scientist, the new technology is proving to be worth its value as failure rates have dipped to near to negligible and productivity has risen by almost 15-20%. His employees can now concentrate better on their work rather than worrying about any Electro-static failures.
Numerous Government labs and defence organizations are now updating and equipping their labs with new cutting-edge technology (Volume ESD) to counter the rising failures due to static energy on work surfaces damaging critical components.
Messung is proud to partner with Defence and other sectors to provide world-class workplace technology solutions in India. The Messung range of Volume ESD laboratory worktables and ESD safe chairs as per IEC 61340-5-1 safety standards, is designed to eliminate risk of electro-static failures and delight users with their smart looks and proven ergonomics.
Author: Mr. Farook Merchant and Mr. Azeem Merchant